Concrete Lifting
Concrete lifting, levelling, void filling and soil stabilization solutions
Concrete lifting & levelling
Polyurethane concrete raising and mudjacking are two methods used to raise and support sunken or unstable concrete slabs, by drilling holes and pumping material under the concrete slab.
How it works
Concrete lifting is the process of raising a slab by injecting stabilizing grout underneath. First, your contractor uses a small drill to create holes in the sunken portion of the slab. Then, they attach a pump which fills the void beneath the slab with material that’s strong enough to raise it back to its original position.
Once the slab is securely in place, they patch and seal the hole and your structure looks as good as new! It’s a straightforward process, and homeowners across the country depend on it for repairs. When you’re trying to decide if it’s the right repair option for you, learning about the pros and cons of concrete lifting can help.
A precise, easy process
Raising concrete with polyurethane foam is done with incremental injections. Lifting foam will fully expand within 10-15 seconds allowing you to monitor the raising and preventing over raising the slab. We suggest using an air-purged gun to deliver foam under the slab. This equipment will keep the injection port open between injections, allowing the foam to fully expand before injecting more foam material.
A quicker, more cost-effective choice
When compared to concrete replacement, the process of raising concrete with polyurethane foam is inexpensive. It is also exponentially faster than replacing concrete. Repaired areas are ready within minutes to be utilized, as they were intended. Polyurethane’s ease of material process and clean-up are some distinct advantages over traditional mudjacking with grout.
Repair Seawalls with HydroFOAM
With every wave, soil washes away and water gets through cracks and gaps in the wall. As cracks and voids form, the wall joints can begin failing. Structural damage may be occurring and a solid foundation will be in jeopardy. You can repair a seawall with HydroFOAM: fill voids, stabilize loose soils and seal leaks at a fraction of the cost of wall replacement. Repairing seawalls with HydroFOAM versus grout or cement doesn’t add weight to a soft soil and the repair will last longer.
Symptoms
- Surrounding ground is mushy or caving in.
- Water is present where it shouldn't be.
- Visible voids and trip hazards.
- Bigger consequences can include foundation issues which will be expensive to fix.
Solution: HydroFOAM
A foam created specifically for applications where water may be present around a concrete slab and/or underneath. HydroFOAM holds up where other brands fail.
HroFOAM is...
- Permanent
- Will not break down in water
- Will not shrink in water
HydroFOAM was specifically developed to resist hydrolysis, a chemical process in which water breaks down foam over time, causing the foam to shrink.
Designed to not only set up in the presence of water, but to maintain dimensional stability. HydroFOAM will plug small holes where water intrusion is present.
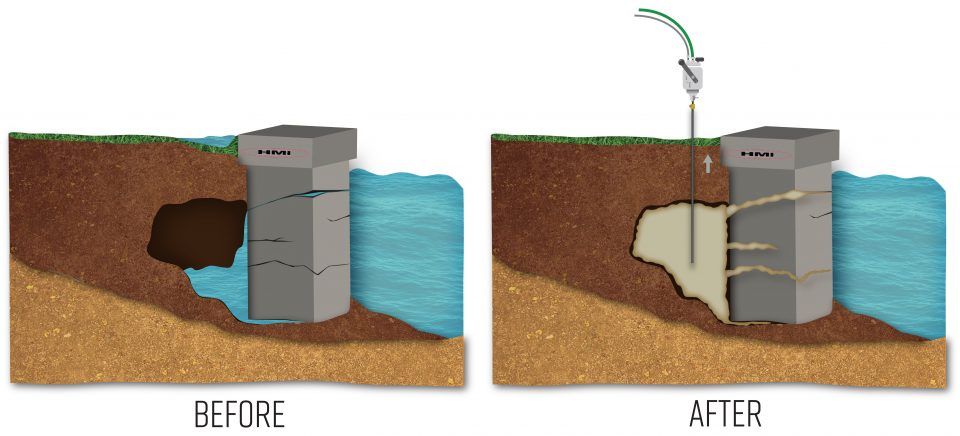